Abstract: Robot welding is commonplace and has penetrated into various industries such as automobiles, electronics, aerospace, and furniture. For complex workpieces, it generally involves collaborative programming and simulation of industrial robots and positioners. Due to its high complexity, it is often laborious and time-consuming. This article mainly introduces how to use the robot offline programming software iRobotCAM to quickly achieve high-precision programming and simulation to meet the high-precision welding of complex workpieces.
The application of robot welding has penetrated into various industries such as automobiles, electronics, aerospace, furniture, etc., and the application scenarios are diverse. From the perspective of the technical evolution roadmap, it mainly includes manual teaching programming, offline programming, and teaching-free programming. If we further summarize and simplify the welding process, it is nothing more than processing the welding trajectory and coordinating the welding process to complete the welding work. From the current industry application of welding, it is nothing more than the following two technical routes:
- Simple welding: Teaching programming becomes history, and teaching-free becomes the mainstream. The application of visual technology, laser tracking technology, etc., also further accelerates the possibility of synchronous coordination of laser positioning and welding, and continuously meets the needs of various segmented welding scenarios.
- Complex welding: generally involves high-precision, positioner collaboration and other scenarios, which tests the control of high-precision trajectories and the process coordination of welding robots to complete complex welding.
With the continuous breakthroughs in domestic industrial software, for the solution to high-precision welding, taking the domestic robot offline programming software iRobotCAM as an example, the CAD-based architecture is chosen to solve complex high-precision trajectory generation and control problems, thereby providing a high-precision solution from the root.
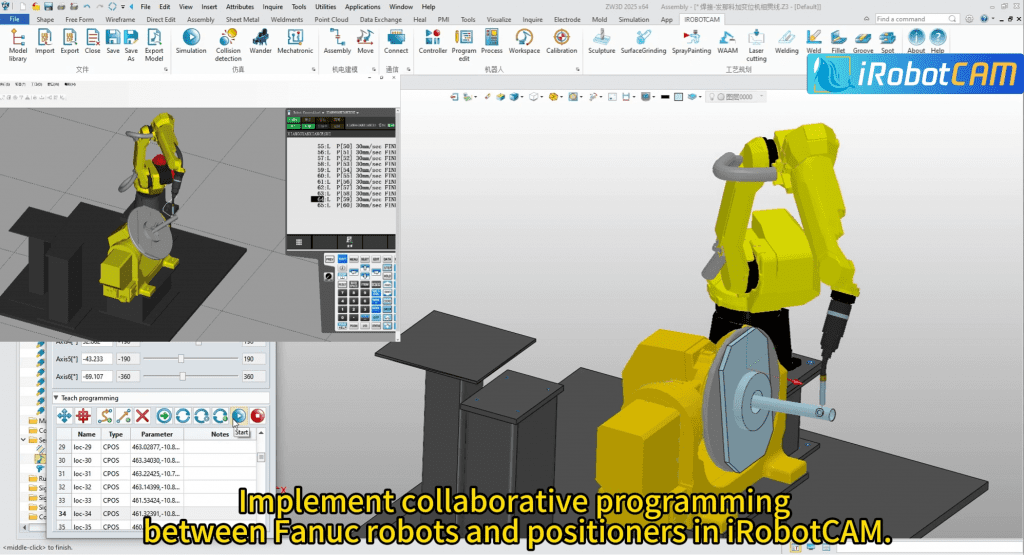
We take the collaborative programming of FANUC industrial robots and positioners as an example to further explain how iRobotCAM realizes welding programming and simulation of complex workpieces.
- iRobotCAM is based on the 3D geometry engine ZW3D, which can generate welds, realize fast or automatic picking of welds, and ensure high-precision weld data.
- iRobotCAM is based on CAM’s five-axis trajectory strategy and rich trajectory methods, which can automatically generate arbitrarily complex welding programming trajectories to meet the needs of various specific trajectories in different industries.
- iRobotCAM, based on the technical architecture of multi-axis linkage and a reliable physical engine, can realize the linkage between industrial robots and positioners, thereby achieving collaborative programming and simulation.
Usability is definitely a key point for complex welding. Through a video, we will explore how iRobotCAM can help you quickly get started with complex parts such as pipe heads, and realize collaborative welding programming and simulation between FANUC industrial robots and positioners.
About Nanjing YueQing Information Technology Co., Ltd.
Nanjing YueQing Technology is committed to building an open iRobotCAM embodied intelligent robot design, programming and simulation platform, which is a digital solution integrating production line electromechanical concept design, offline programming, virtual commissioning, and robot modeling and training.
iRobotCAM website: www.iRobotCAM.com, contact email: cooperation@iRobotCAM.com